Products Details
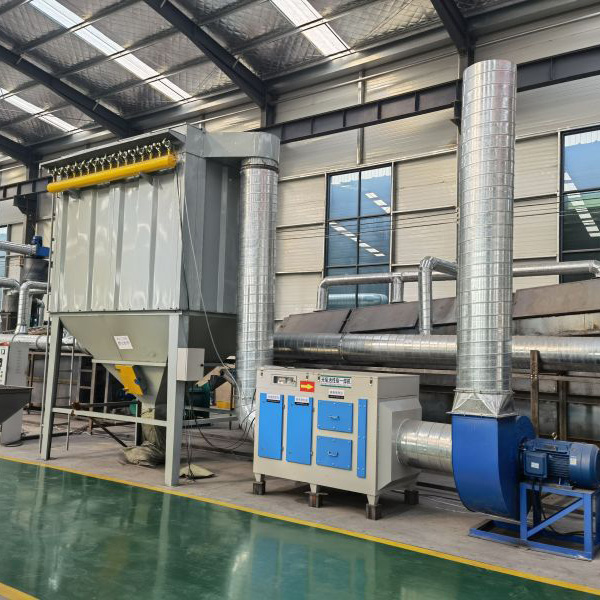
Product Description The waste lithium battery recycling and processing equipment separates the waste lithium battery into the raw materials we need by separating and regenerating the waste lithium battery. The facility is used for separation treatment, and there are pulse dust removal facilities to collect the dust generated during the separation process and subsequent processes. To form a green, high-quality closed-circuit cycle system for the whole life cycle of the battery, the waste lithium battery recycling and processing equipment mainly uses the aluminum foil, copper foil and positive and negative electrode materials in the positive and negative plates of the discarded lithium battery to separate and process for recycling. The development environment of the industry is optimized, and the development prospect of lithium battery resource utilization is considerable. 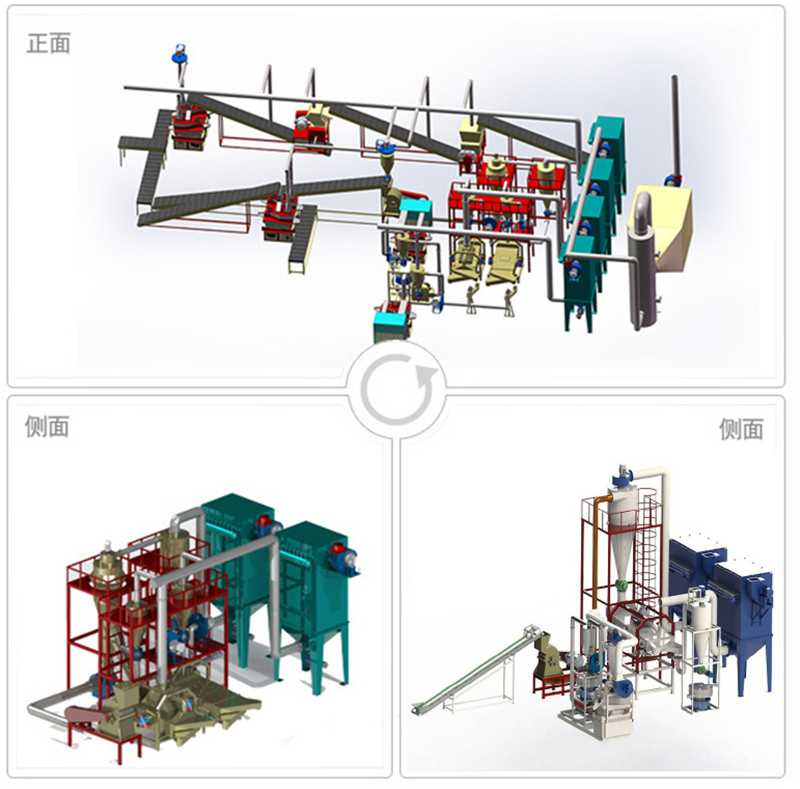
Features: 1. The resource utilization of metal copper and carbon powder in waste lithium battery materials can be realized through the combined process of hammer crushing, vibration screening and air separation; 2. The material can be effectively peeled off between the carbon powder and the copper foil after being crushed by hammer vibration, and then the copper foil and the carbon powder can be preliminarily separated by vibration sieving based on the difference in size and shape between the particles; 3. For crushed particles with a particle size of 0.125~0.250mm and a low copper grade, air separation can be used to achieve effective separation between copper and carbon powder. When the air velocity is 1.00M/S, a good recovery effect can be achieved. ; 4. This equipment is mainly used for lithium-ion battery manufacturers to separate and process the aluminum foil, copper foil and middle and negative electrode materials in the scrapped positive and negative electrodes for the purpose of recycling. The complete set of equipment operates in negative pressure without dust leakage, and the separation efficiency can reach more than 90%.
CNC Punching Machine,
Plastic Gold Metallizing,
Small Concrete Block Machine,
Upvc Roof Sheet,
Phosphogypsum Powder Machine,
Saw Dust Briquettes,
Pir Sandwich Panel,
Gypsum Board On Concrete Wall,
Acrylic Sheet Bending Machine,
Pvc Sheet Production Line,